THE CONCEPT AND BRILLIANCE OF 5-AXIS MACHINING has long been the ability to completely machine a part in one setup, or very close to completion. In our company’s machine tool world of critical, heavy-duty, highly accurate parts, the machines were quite large as well. What has evolved is 5-axis work produces more parts, customer companies are growing, and they need to accommodate all the new orders.
Sounds wonderful, right? The theory of 5-axis is paying off. To accommodate growth, manufacturers need more machines—but there’s no more space on the factory floor and expansion is out of the question for most. Companies seem to be victimized by their own success in applying the latest machining strategies.
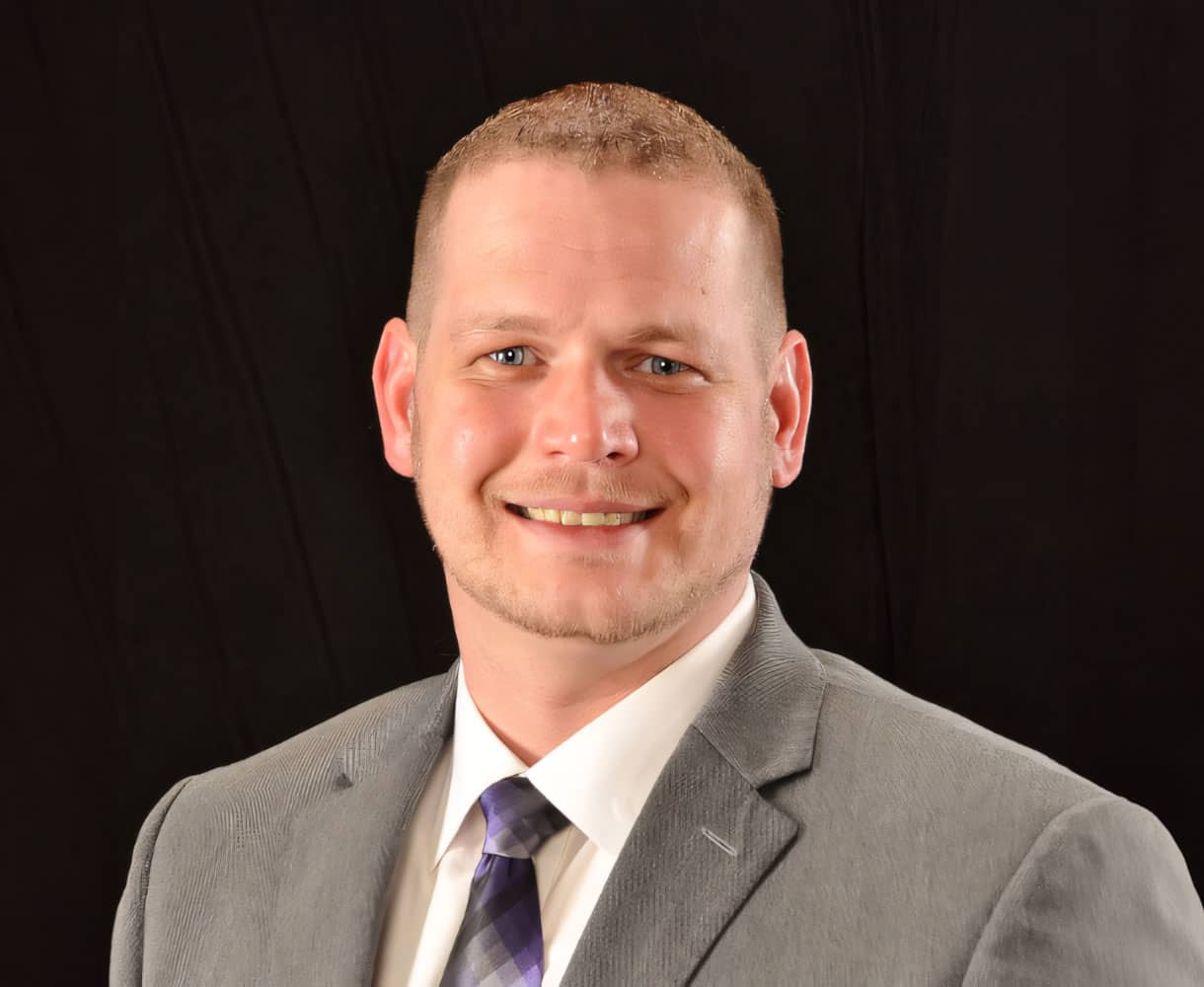
Happily, there is a solution. Machine tool builders are in continual communication with customers and have recognized this trend evolving over the last several years. Our customers have been direct, asserting, “We need to do more in a smaller footprint,” or asking, “Can we replace these two machines with three in the same real estate?” One of the most common questions I hear is, “Is it possible to get a bigger workpiece in this same machine?”
Of course, any good salesperson wants to say, “Yes, we can help you do that.” To that end, our company has developed smaller 5-axis machine platforms that are robust and accurate, capable of doing heavy cutting, and, while they are about one-third the size of our larger legacy models, their work zone can accommodate large parts.
Most customized machine-tool builders start by understanding the customer’s needs. We want to understand the parts, but machine tool companies aren’t always the best at making them. The more you can relay to your builder partner, the better the result will be. What is the material? Do they have complex geometries? What are the dimensions and tolerances? What volumes are we talking about? Our engineers then take a machine tool platform and see how it can be adjusted to the customer’s needs, whether it be a higher power spindle while taking into consideration the rigidity requirements to be able to support the new spindle, or how to get more space in the work zone without extending the footprint.
Perhaps we need to adjust our casting a little bit or move some components around to fit more machines closer together in a given space, like a puzzle. Perhaps a gear table is best for the application or maybe a direct-drive motor table. Perhaps the high torque spindle is ideal at 15,000 rpm or maybe it should be 30,000 rpm. Can the spindle taper be adjusted? There are myriad choices if the machine is built to accommodate that sort of customization. Platform flexibility and interchangeability are key to a successful design and result.
Applying new machining strategies also can help customers get more production out of the machines they have in an allotted space. The control systems, too, are advancing to be ever smarter and more intuitive, which enables fine-tuning processes and boosting output. For example, we frequently tune for heavy hogging, and in grinding we’ve done a lot of special applications to perform at an optimal ability just by understanding the nuances of the control system’s algorithms. Five-axis machining has lived up to its promise.
Manufacturers are incredibly productive, many to the point where the opportunity for growth is outpacing their physical space capacity. Companies need to use the floor space they have to the utmost efficiency. It’s been a particular challenge to get more productivity out of their heavy-duty category of machines, which are usually large units, or replace them with more, smaller machines to drive up output. Creative builders with sound engineering are answering that challenge.